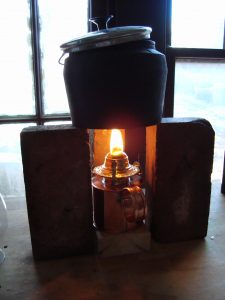
Although my shop conversion began in 2005, most of the processes I’ve used over the last 30 years involve hand-tools. Before the power outage in 2008, I always had access to electric power in the shop. Electricity was always there to tackle a job I was capable of, but just didn’t feel like doing at the time…like hand-sawing through 12/4 stock, or regulating the heat on a glue pot or bending iron. The little copper oil lamp’s flame changed my mind for the better. It convinced me that not only was it possible to lose reliance on power tools, but for me, it was a necessary step in my shop’s evolution and in my craft.
The cast iron glue pot and oil lamp worked very well, and for case-making or carpentry, I wouldn’t hesitate to use that setup again. Cast iron glue pots and oil lamps have two side effects that have their place in woodworking, but aren’t always welcome in instrument making: a) water from the glue pot’s iron stains wood, and; b) oil lamps produce soot. Iron as a stain is great, but it also darkens hide glue. I usually got around this by using a glass baby-food jar inside the gluepot surrounded by a second water bath surrounding the jar, and for cleaning up excess glue. Unfortunately, the second water bath was also exposed to iron, so it would also stain any light wood it contacted.
Recently, I ran across Martin Shepherd’s antique piano tools page. His glue pot and bow drill pages immediately stood out, as they represented two of the last three process I have left to convert in my shop (glue pot, in-situ bridge drilling, and side/rib bending). His “Glue Pots” page, introduced me to globular copper glue pots (pot de colle), that were produced in Villedieu-les-Poêles, from the end of the 18th century, until WWII. After scouring eBay for a few months, I found a pair of glue pots for my shop. The first pot I found, was a small (the same size as my Hold Heet), highly polished example with beautiful hammer marks, but due to some stress cracking (due to a fall sometime in the last 70 years), it will need some dovetailed patching before being put back into use.
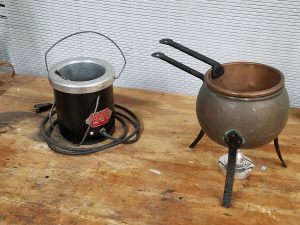
With the second example, I found the verdigris covered, pot de colle of my dreams. It’s a big glue pot, and it’s finish level was never taken beyond pickling and scraping off the fire and hammer scale. I often see glue pots of this size described as cabinet maker’s or carpenter’s pots, and only the smaller ones being offered with any connection to luthiery. I think that is due mostly to a modern mis-understanding that hot hide glue is always applied sparingly. I used to think the same way, until reading David Van Edwards’ “Build Your Own Renaissance Lute” course. While I still make small batches of glue, it gets liberally applied to hold in the heat until it sets. I also believe now that an abundance of hot water can be a great thing to have on hand when building instruments. This example holds about .8 Gallons/3.03 Litres of water.
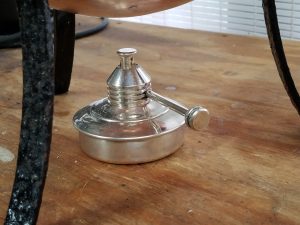
While the tall Villedieu pots work equally well with oil or spirit lamps, I followed Mr. Shepherd’s lead, and opted for a small alcohol-powered chafing dish burner as a heat source. Alcohol is a little easier to deal with in the shop, doesn’t stain like lamp oil if spilled, and produces almost no soot. Another trip to eBay secured a little Sheridan chafing dish burner, with an adjustable wick and built in snuffer.
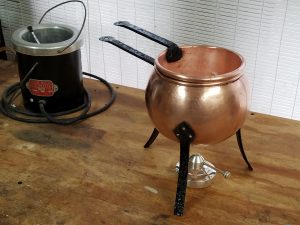
A bag of lemons, a generous amount of table salt, and some elbow grease later, and the copper pot was ready to prove its worth. I had some doubts about the little Sheridan burner’s ability to heat such a large pot. Almost a gallon of water later, and the burner filled with denatured alcohol. I was ready to make my first batch of glue.
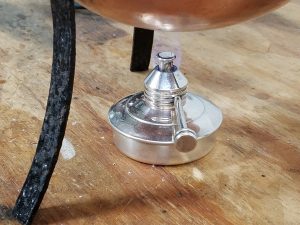
After lighting the burner, it took about 15 minutes for the pot to reach 140 degrees Farenheit…which is about the same amount of time my electric glue pot takes. I really questioned whether the lime-putty lining in the outer pot was an original feature, and whether it would still be there after a glue-making session, but I’m happy to report that the pot works wonderfully. While it the volume of water makes changing temperature a slow process, the temperature is still very easy to modulate.
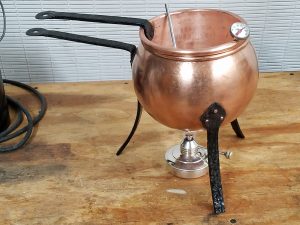
I couldn’t be happier with the outcome. Once it’s adjusted and at working temperature, the Villedieu pot holds the glue and water bath at a rock-solid 140 degrees Farenheit. Further testing during my first glue making session also showed another advantage of the pot’s design: the interior lining and large volume of water hold heat for a very long time after the flame is snuffed out. This means that the pot can be heated up, and gluing done without the flame being lit. My tests in a 60 degree Farenheit shop showed that the glue stayed in a working temperature range for up to 13 minutes after the flame was extinguished.
You must be logged in to post a comment. Login